FDM Printing
FDM printing is one of the fastest available options for additive manufacturing.
But you can’t get the quickest turnaround without a strong team of experienced engineers and a global support system dedicated to delivering your part.
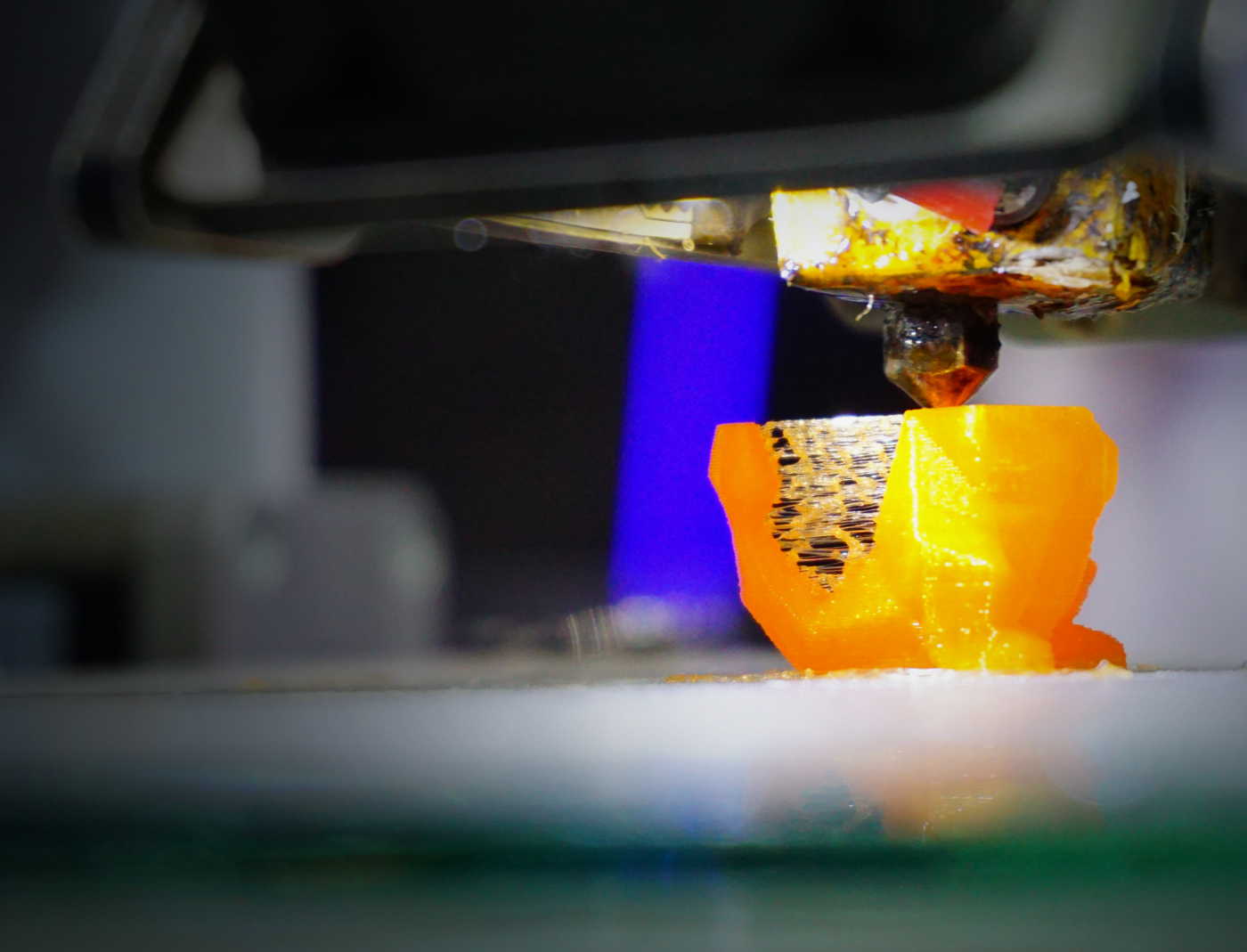
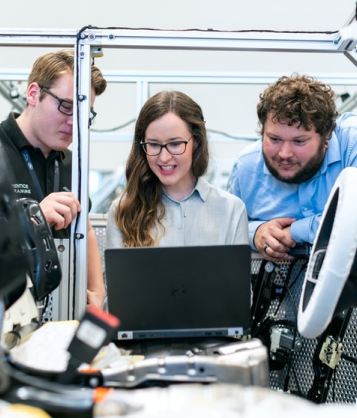
Quickparts has historical experience, highly trained professionals, and facilities stationed around the world to support FDM printing that deliver quality parts and prototypes to fit your needs.
How it Works
As opposed to other additive manufacturing techniques that use lasers or lights on material particles, FDM printing is a solid-based rapid prototyping method. The printer builds parts in an additive process that extrudes material layer by layer to build a model.
This enables cost-effective parts and complex geometries that are often difficult to duplicate with traditional manufacturing methods.
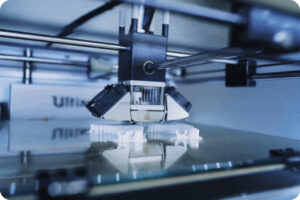
Let us be your resource to determine which manufacturing process is right for your project.
About Quickparts
Quickparts is a pioneer in the 3D printing world.
We are the originator of a full digital manufacturing platform that delivers on-demand additive and traditional manufacturing services. From rapid prototyping to appearance models and volume production, Quickparts operates the most advanced technology and possesses the expertise to handle any additive manufacturing project.
With facilities stationed around the world, each staffed with experienced engineers laser-focused on meeting your specific requirements as effectively and quickly as possible, you can trust Quickparts with all of your manufacturing needs.
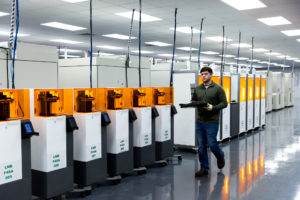
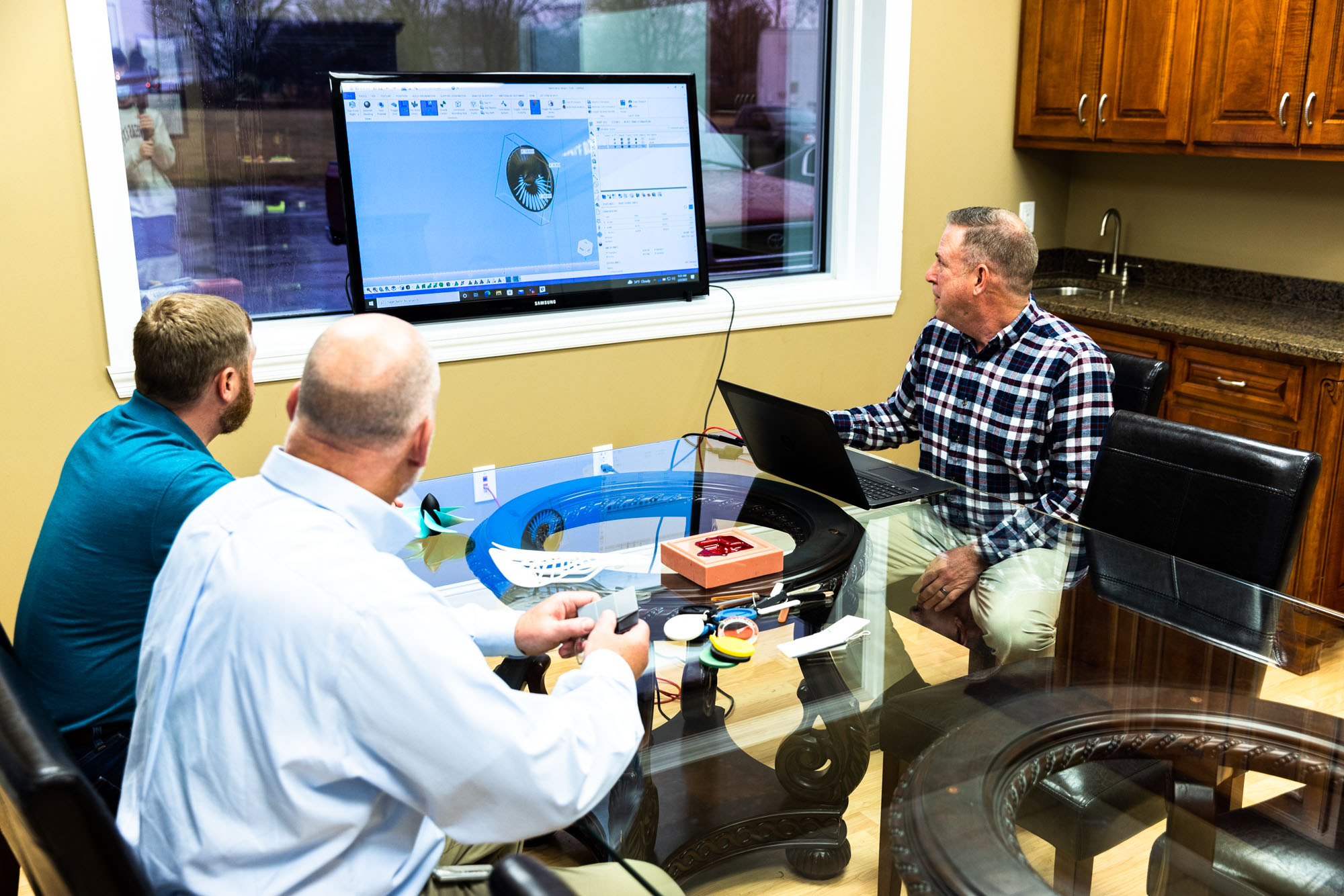
Get Started
You’re seconds away from starting your Quickparts project.
FDM 3D Printing Services- Quality Products At The Most Affordable Price
Do you need to print large parts with high accuracy? Quickparts has expert capabilities with Fused Deposition Modeling to deliver low-volume production 3D parts. By choosing us, you can get the ideal prototype of your product and utilize the benefits of our innovative solutions to get your product in hand fast.
We understand FDM 3D printing principles
The FDM 3D printing process involves material extrusion. A spool passes the thermoplastic wire through an extruder that not only heats but also melts plastic. Filaments are found with a diameter ranging from 1.75 mm to 2.85 mm. The diameter of our standard nozzles is 0.4 mm.
The nozzle and extruder create the print head moving along the plate to form every layer. It follows instructions from a file containing a sliced 3D version.
There is a unique layer for every slice. So, we make more slices for a taller object. Our company has invested in high-quality printers that offer a layer with a standard thickness. The plastic melting onto the previous layer gets hardened using a cooling fan.
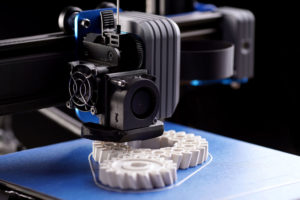
Get the best filament-based 3-dimensional printing solutions
Our professionals are efficient at dealing with the FDM manufacturing process. We focus on different features like power recovery, bed leveling, and closed-build chambers. Our professionals work with the latest technologies used for low-volume production and rapid prototyping.
It is true that FDM printing can cause rough surface finishes. However, we are able to manage it efficiently. We can overcome challenges like tumbling, sanding, and vapor smoothing as we rely on innovative methods.
We pick the right materials
Our specially designed FDM 3D printers use different thermoplastics. We have found it easy to print the biodegradable thermoplastic polylactic acid. It provides an affordable and fast solution for you. We have also worked on highly durable materials, like ABS, chosen for various items (such as laptop keys).
Our company has designed a variety of FDM parts, from enclosures to prosthetics.
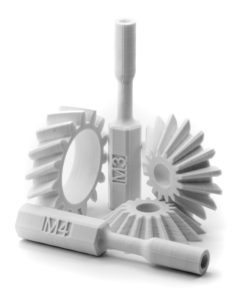
Why do our clients prefer FDM technology?
- FDM fused deposition modeling technology is easy to use.
- It reduces the production cost associated with 3D printing technology.
- The lead times for this manufacturing process are comparatively shorter.
- It is easy to deal with complicated cavities and geometries with FDM technology.
- There are several high-performance options that need element resistances.
- Our professionals can produce on-demand parts.
Each prototype uses FDM technology in the 3D printing project to include the build speed, platform temperatures, cooling fan speed, and layer speed.
Are you ready to submit your project now? Click here to get started on your fused deposition modeling 3D printed product.