We do all kinds of 3D printing work -- concept modeling, verification, prototyping -- but direct digital manufacturing of end-use parts is the biggest opportunity
Joe Carmody takes pride in all of his company's 3D printing work for Nissan Motorsports (NISMO), but his biggest passion is direct digital manufacturing of parts that sometimes go from concept to the race track within a week. It's there, literally, where the rubber meets the road.
Direct digital manufacturing, also called additive manufacturing, is the process of 3D printing a working part layer by layer directly from a digital file.
"We do all kinds of 3D printing work -- concept modeling, verification, prototyping -- but direct digital manufacturing of end-use parts is the biggest opportunity," says Carmody, president of evok3d, co-housed in the Nissan NISMO facility outside Melbourne, Australia.
evok3d produces its bespoke parts for Nissan using various 3D printers, including a 3D Systems ProJet 660Pro for conceptual and prototyping work and ProJet MJP Plastic additive manufacturing and industrial SLS systems for high-precision, functional parts that prove their mettle in the V8 Supercar Championship series. The 15-round Australian racing series comprises two types of races -- sprint and endurance -- providing a diverse set of challenges for competitors.
Closing the experience gap
Most of the work occurs in the heat of the racing schedule, when adjustments are made in the so-called downtime between races, which can be anywhere from a week to four weeks. It's not just a matter of increasing speed, but continuously improving reliability and finding out how to eliminate or reduce malfunctions -- both human and machine.
"Direct digital manufacturing is ideal for racing applications, which require that cars are continuously improved and component designs iterated upon within small timeframes," says Carmody.
For Nissan NISMO teams, the learning curve is steep and fast. Nissan started racing in V8 Supercar in 2013. It is competing against other teams that have raced in the series since its inception as the Australian Touring Car Championship in 1993. There's a lot of catching up to do, and 3D printing is seen as a key tool in closing the experience gap.
Gurney flap in three days
Shortly after signing on with Nissan NISMO, the team faced an immediate challenge: improving the aerodynamics of Nissan Altima racecars. The rear wing wasn't generating enough down force, which hindered cornering ability and speed. Nissan engineers went to work and developed what is known as a gurney flap -- a small, curved strip extending off the rear trunk that, if done right, can dramatically improve aerodynamics.
"It's a complex piece of geometry," says Carmody, "with compound curves that would be difficult to manufacture using traditional modes."
After receiving the design files from Nissan, the team went to work producing the part on the ProJet MJP 3D printer. Introduced in early 2013, the printer is designed to produce functional plastic parts and investment casting wax patterns for professional-grade design and manufacturing applications.
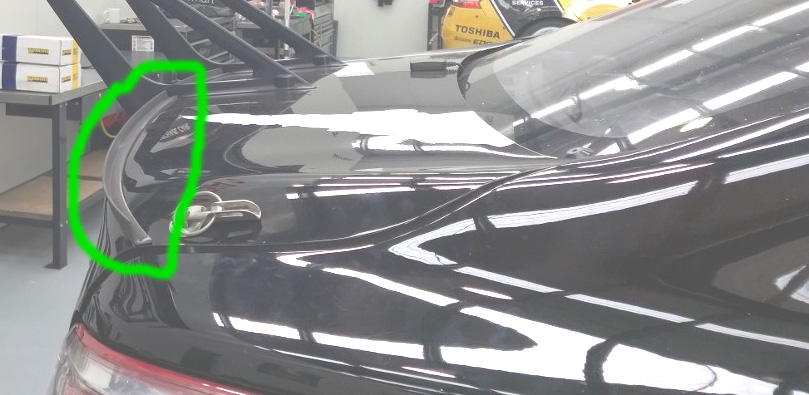
The gurney flap was printed in 3D Systems VisiJet M3 Black material, a durable plastic that looks and feels like injection-molded plastic and is designed for applications requiring snap-fit and strength.
Redefining the timeframe from design to race-car-ready, the gurney flap was manufactured and fitted onto the race car for testing within three days. The new part reduced drag on the rear of the car and increased down force, helping the Nissan Altimas achieve the highest corner speeds of any cars in the V8 Supercar Championship series.
Keeping the air flowing
Soon after, the team put its direct manufacturing abilities to work on a driver cooling system. Track temperatures at V8 Supercar venues can reach 100 degrees Fahrenheit and top 150 degrees inside the racecar, making it critical that the driver cooling system operates continuously and reliably.
A key component of the cooling system is the air feed to the driver's helmet. The system comprises a dry ice box to cool the air, a filter to clean the air, a pump to generate airflow, and ducting to conduct cool air into the driver's helmet.
evok3d's assignment was to build a lightweight, one-piece housing for the air pump. It might sound simple, but achieving the right combination of weight, functionality and reliability isn't an easy engineering task.
"It would be difficult to manufacture in a single piece using subtractive or injection manufacturing processes," says Carmody, "but we were able to support the overall design goals by creating a single piece using the ProJet MJP with VisiJet M3 Black material that provides the flexibility and strength required for a production part."

Another inside-the-car project involved a fan housing with an integrated vane switch that allows the driver to manually control air flow between his foot well and the windshield if it is raining. The assembly was printed on a high-definition SLS machine in DuraForm material with all moving parts in place except for the motor and the fan. DuraForm is designed to generate smooth wall surfaces and strength equal to or better than an injection-molded part.
"All three of these parts have proven successful and are currently being used by the Nissan team in the V8 Supercar Championship series," says Carmody.
A different landscape
While Carmody sees direct digital manufacturing as the biggest opportunity for 3D printing, there is also great value in generating small-volume parts for concept modeling, prototyping and pre-production.
evok3d has used the ProJet 660Pro printer to create a complex mold for an air intake system and the master of a carbon fiber gear-shift cover that helps prevent drivers from accidentally putting the race car into gear during driver changes in endurance races.
Carmody believes that many of the prototypes evok3d now creates will eventually be printed as production parts as costs continue to spiral downward and new design techniques are adopted.
"Designing for 3D-printed parts presents a whole different landscape for engineers who have designed for traditional manufacturing," he says. "But there is great value in being able to unitize parts, eliminate assembly, reduce weight and increase efficiency through 3D printing. Direct digital manufacturing enables you to place material exactly where you want it for maximum performance and reliability."
If the results from the Nissan Altima V8 Supercar racing teams are any indication, the movement toward direct digital manufacturing will continue to pick up momentum. In only the second season on the circuit, Nissan teams are belying their relative inexperience, with two of them in the top 10 in standings.
The fast-track success isn't surprising to Joe Carmody. He'll tell you that the best is yet to come for both direct digital manufacturing and Nissan NISMO's V8 Supercar teams.
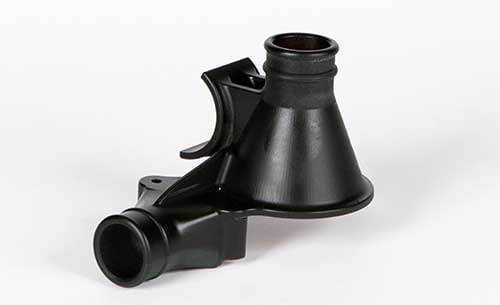